7 Kpis to Identify and Address Operational Bottlenecks in Your Business
In the fast-paced world of operations, identifying bottlenecks is crucial to maintaining efficiency and productivity. This Q&A style blog post uncovers seven insightful KPIs that can pinpoint these operational challenges. The discussion kicks off with the importance of measuring Average Job Completion Time and wraps up with assessing On-Time Delivery Performance. Dive in to explore all seven key metrics and see how they can transform operational workflows.
- Measure Average Job Completion Time
- Track Job Completion Versus Estimates
- Monitor Cycle Time Variability
- Analyze Defect Ratios by Process Step
- Track Work-in-Progress Inventory Levels
- Measure Resource Utilization
- Assess On-Time Delivery Performance
Measure Average Job Completion Time
One KPI that has been particularly helpful in identifying bottlenecks in our tree-service operations is Average Job Completion Time. This KPI measures the time it takes from the moment a crew arrives on-site to when they wrap up a job, which directly reflects productivity and highlights where delays might be occurring. A few years ago, we noticed that some of our jobs were running over the estimated times. By breaking down this KPI further, we identified that delays stemmed from a specific step in equipment setup. Crews were spending more time preparing than anticipated due to inconsistent tool placement in our trucks. This insight led us to restructure how equipment was organized, ensuring that tools needed first on a job were placed for quick access. Since then, job times have become more predictable, and we reduced setup time, allowing us to handle more jobs each week.
My long years of industry experience were invaluable in making these improvements because I know the field firsthand and understand how small operational changes can impact the whole day. As a certified arborist and TRAQ-certified professional, I'm able to assess job-specific needs quickly, which helped us create an equipment layout that speeds up site preparation without sacrificing safety. This focus on efficiency and precision not only improved our team's workflow but also translated into better customer satisfaction as we could complete projects faster and exceed expectations on timing.
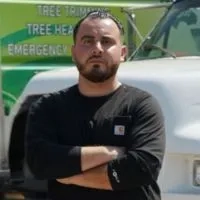
Track Job Completion Versus Estimates
One KPI that's been particularly effective for me in identifying operational bottlenecks is the job completion time versus estimated time metric. By tracking how long each job actually takes compared to our initial estimates, I can quickly spot areas where we may be underestimating or overestimating time requirements. For example, during peak season, I noticed that some garden-maintenance jobs were consistently taking longer than anticipated. By drilling down into these discrepancies, I identified that the bottleneck was often in prep work and equipment setup, especially for larger properties with more complex landscapes. My experience in horticulture allowed me to assess which tasks required additional hands-on care, and I was able to streamline our approach by ensuring we had the right tools and a clear setup process for each site.
In one case, a client with a sprawling garden featuring intricate beds and a variety of plant species was experiencing service delays. By adjusting our prep process, allocating specific tools for each area, and having a clear flow for each task, we reduced job time. My background in plant care and my understanding of efficient landscaping practices meant that I could make these tweaks with confidence. Not only did this improve our efficiency, but it also led to higher customer satisfaction, as we could meet our promised timelines more consistently. This KPI-driven approach has been invaluable in making our operations smoother, helping us deliver top-notch service to every client.
Monitor Cycle Time Variability
It's important to keep an eye on cycle time variability, as this can highlight areas where your process is slowing down. Variability in cycle time can indicate issues in workflow or task execution. By reducing these variabilities, the overall process efficiency can be improved.
This metric helps in understanding how consistent the process is. Analyzing cycle time variability helps in optimizing the process flow. Start monitoring cycle times to enhance your process flow now.
Analyze Defect Ratios by Process Step
Another key metric to examine is defect ratios by each process step. Identifying which steps produce the most defects can uncover problem areas. This helps in addressing the root cause of the defects, rather than just treating the symptoms.
It ensures higher quality output and fewer reworks. Analyzing defects can improve product quality and process efficiency. Take action to analyze defect ratios in your process today.
Track Work-in-Progress Inventory Levels
Tracking work-in-progress inventory levels for each stage of production can reveal where delays occur. Knowing the bottleneck stages ensures better management and resource distribution. High levels of work-in-progress inventory may signify issues with workflow efficiency.
By addressing these delays, overall productivity can be increased. This can help streamline production and prevent backlog accumulation. Begin tracking your work-in-progress inventory levels for better workflow management.
Measure Resource Utilization
Measuring resource utilization is crucial to finding overloads or underutilization in your workforce. High levels of resource utilization can indicate overworked employees or equipment, leading to burnout or breakdowns. On the other hand, underutilization reveals inefficiencies where resources are not used to their full potential.
Balancing resource utilization maintains workflow efficiency and employee satisfaction. Optimal resource use boosts productivity and morale. Make it a priority to measure and adjust resource utilization to improve efficiency.
Assess On-Time Delivery Performance
Assessing on-time delivery performance is essential for understanding workflow efficiency. This metric shows how well the existing processes meet deadlines. Consistent delays in delivery might indicate deeper issues such as inefficient processes or resource blockages.
Improving on-time delivery helps in satisfying customers and maintaining a competitive edge. It highlights the need for timely production and delivery processes. Focus on improving your on-time delivery performance to enhance customer satisfaction.